Leonhard Weiss
Standardized telematics for a mixed fleet of machines – How LEONHARD WEISS Construction Company optimizes the efficiency and management of its machines by using AEMP data in combination with the Simple Tracker.
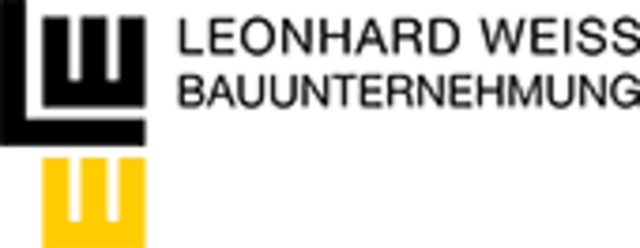
Customer
Leonhard Weiss Construction Company
Solution
Mixed Fleet Telematics & Simple Tracker
Industry
Construction Company
One fleet – different manufacturers
LEONHARD WEISS, a leading German construction company, faced a significant challenge that many machine owners are familiar with: Integrating machine data from different manufacturers on a standardized data platform. This usually poses two problems:
On the one hand, construction companies usually use machines from different manufacturers, some of which are not equipped with telematics solutions at all. On the other hand, the machine manufacturers who equip their machines with telematics usually have their own data portals to view the data and information. However, managing multiple data portals leads to inefficient data management and additional time and costs for the operator of the mixed fleet. LEONHARD WEISS, therefore, wanted to use a single platform to monitor its entire fleet of machines in order to reduce operating costs and increase efficiency.
The challenge of telematics integration in mixed fleets
The integration of telematics systems was complicated due to the OEM’s different standards and signal types of the OEMs. Although the ISO15143 standard now exists, it is not yet fully or uniformly implemented by all manufacturers.
A major challenge for LEONHARD WEISS was that the value "operating hours", for example, was interpreted differently by each OEM, and the frequency of signal transmission varied, resulting in incomparable and inconsistent data. Under these conditions, standardizing telematics data from different manufacturers became extremely time-consuming and cost-intensive. In addition, machines without a telematics solution continued to be disregarded. In addition to the OEMs' inconsistent interpretation of the ISO15143 standard, LEONHARD WEISS wanted to map smaller machines and other assets, such as skips and power generators, in a single portal.
These hurdles made it difficult for LEONHARD WEISS to utilize the telematics data for operational processes and implement automation. A practicable approach had to be found to ensure a cost-efficient and timely solution for the entire fleet.
Simple Tracker brings all machines onto one platform
LEONHARD WEISS, therefore, decided to implement Simple Trackers on machines without a telematics solution to record their operating data and locations. These trackers transmit basic signals such as geolocation and operating hours, which are sufficient for scheduling and maintenance planning in the first step. A significant advantage of Simple Trackers is that they are easy to retrofit, as they are easy to install and can be quickly fitted in LEONHARD WEISS workshops.
These trackers allow maintenance cycles to be optimized accordingly based on the operating hours recorded. The location data from the trackers also significantly improves machine scheduling. Machines can be moved more easily between construction sites as their position can be found quickly and transported quickly if necessary, which is particularly advantageous on large construction sites.
Another advantage is linking attachments, such as excavator buckets, equipped with beacons that constantly transmit a Bluetooth signal. The trackers record these signals and transmit them to the portal, which allows one to track which attachment tools belong to which machine and where they are located.
Optimized machine management through trackers
Thanks to trackers and beacons, LEONHARD WEISS can now seamlessly integrate the telematics data of all machines into its central data platform and thus also utilize a large part of the DataPortal's features.
In this way, LEONHARD WEISS improves logistics and the utilization of construction machinery on construction sites. The workshops can also proactively plan maintenance and procure spare parts in good time, which helps to reduce downtimes and increase machine availability. Thanks to the location data, machines can be approached directly, saving time and resources.