The digitization challenge in the construction industry
This article demonstrates that digitizing processes in the construction industry requires a solution capable of handling multiple types of assets tracked by numerous kinds of devices. Additionally, it explains why retrofitted solutions are not the way to go.
The digitization challenge
The rise of IoT, telematics, and Industry 4.0 has opened new opportunities to digitize entire industries and make them more efficient. In general, digitization allows collecting real-time data from every component participating in creating value within an industry to make operational, tactical, and strategic decisions made on facts available timely, resulting in better business outcomes.
But, as Professor Jeronimo van Schendel, Director of the Master in Business for Architecture and Design at IE, puts it: "the construction industry is lagging behind almost all other industries when it comes to digitization". He also points out possible causes for this delay: "The delay in embracing digitization is not due solely to cultural factors. Roadblocks are inherent to the construction industry, with its disaggregated value chains, a strong physical work component and high risk embedded in its operations".
This lack of digitization leads to that companies are making decisions based on inaccurate or outdated information, which results in poorer business outcomes.
This article shows how companies in the construction industry can achieve quick wins by digitizing part of their business using ready-to-use telematics data from construction equipment.
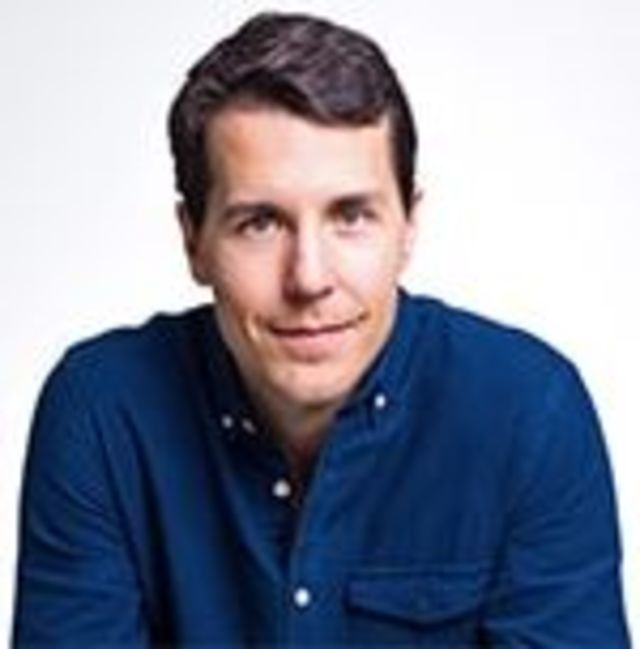
Jerónimo van Schendel Erice
Someone already digitized your excavator
It is not a surprise to people in Head of Machine Technology or Head Operations roles in construction companies that some of the heavy equipment they own is IoT-enabled and captures operational data from the machine and sends it to the OEM.
Furthermore, suppose you own this kind of equipment. In that case, you may be already paying your dealer for a telematics contract that entitles you to access this data through an OEM's proprietary solution.
If you are wondering what kind of information is already digitized in your equipment, ask your OEM, but in most cases, you should get:
- location
- total distance traveled
- total operating hours
- total idling hours
- total fuel consumed
- fuel level
- diesel exhaust fluid level
Review your equipment contracts and check what you are paying for!

How to improve a business process with digitization
"So what can I do with the telematics data that I'm getting from my machines?" - Let's look at three quick wins where you could use the basic telematics data provided by your OEM that will provide great business outcomes without significant investments.
All three quick wins focus on reducing machine downtime or increasing its utilization and resulting in a more robust bottom line.
Machine Scheduling & Dispatching
One of the most straightforward pieces of data you get with your telematics is the latest known location of your machine. And one of the needs of your company is being able to move your machines to the worksites where they are most needed.
It is a failure not to have up-to-date and accurate locations of your equipment. Because it results in lost equipment and equipment that can not reach the target worksites in time, this, in turn, causes delays in the construction works, which reduce profits.
Accurately tracking where your equipment is located and sharing this information with the team responsible for fetching the equipment and dispatching it to a different worksite is critical.
Fuel Delivery
Fuel is what keeps your equipment running, so missing to deliver the right amount of energy in time to the correct worksite could leave your equipment stalled, and your project is not progressing as expected.
Looking at your fleet's fuel consumption and fuel tank levels at the end of the day will help you plan how much fuel to deliver to each worksite the next day. Your decision will be based on facts, not guessing. This opportunity ensures your operations are non-stop and that there will be no stalled machines because they are waiting for the next fuel delivery.
Maintenance
Failure to adhere to scheduled maintenance requirements for your equipment is a significant source of machine downtime and workplace safety hazards. This unexpected downtime is one of the biggest contributing factors to project delays. Just by making sure the OEM services each of your machines, you can eliminate downtime and safety risks with the same shot.
Luckily for you, your OEM's telematics is already delivering the operating hours of your machine and its location. Just operating hours data is enough to plan your scheduled maintenance before the next service cycle is due. Sum up the machine's location to the information cocktail, and service technicians will easily find the machine they need to service when it needs to be serviced.
It is easy to eliminate machine downtime due to overdue or skipped maintenance, putting the most noticeable project delays to an end and improving your bottom line.
How much does it cost? How long does it take?
The implementation of the Quick Wins explained here should take between 3 and 6 months. Usually, it requires no to very little investment.
Implementing these quick wins work best when:
- managed as project
- you have good connections inside the company acting as partners in the key areas your project touches
These quick wins pay off by themselves. Our cost-saving estimate starts at 600 € per machine per year. The estimation is based on real-life experience in digitizing machine planning and scheduling, fuel delivery, and maintenance. Only the effects on the standstill of the operation because the machines did not arrive on time at the place of operation, the machines were not refueled or serviced on time are objectively considered.
Conclusions
When looking at digitization projects, it is easy to overlook that most of the heavy equipment owned by construction companies is already IoT-enabled by the OEM and that you may be already paying to have access to your fleet's telematics data.
You should check your existing contracts with your dealer and verify whether you already signed up for telematics or if you need to increase the scope of your current arrangements.
Then, choose a part of a business process you would like to digitize or pick one of the quick wins shown in this article. In less than six months, you should implement one of the quick wins, if not all three, and enjoy the cost savings they will deliver.
Let's talk about your business and see how we can implement quick wins.
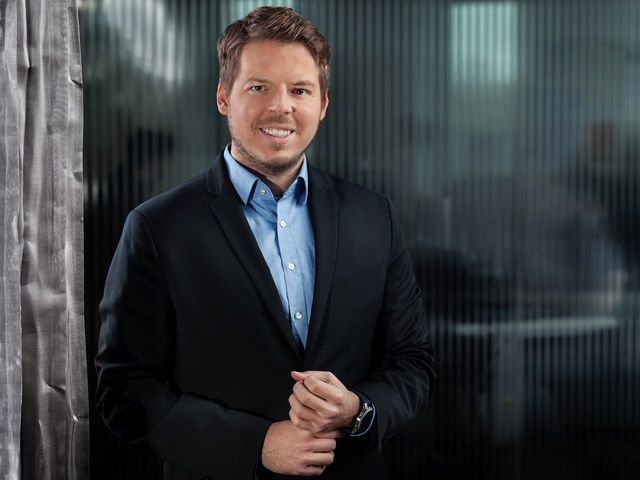