Cut downtime in half with online maintenance planning
Are outdated paper-based maintenance systems holding you and your customers back? Many OEMs still rely on manual or semi-digital processes to plan and track machine maintenance, leaving room for error and guesswork. But there is a more efficient way — online maintenance planning can revolutionize how you manage machine upkeep, reduce downtime, and save your customers money.
Paper-based systems cause unnecessary downtime
Using paper or semi-digital records to track maintenance means relying on rough estimates, leaving maintenance schedules vulnerable to being missed. Without real-time machine data, operating hours can go unchecked, leading to unexpected breakdowns, expensive repairs, and costly machine downtime.
Digitize maintenance to maximize machine uptime
Moving to an online, data-driven maintenance system can cut downtime by up to 50%. With Proemion’s DataPortal and DataPlatform, OEMs and dealers can transform after-sales service by tapping into live machine data. This allows you to track machine use, anticipate when maintenance is needed, and notify customers ahead of time. You can even schedule service technicians before issues arise, ensuring machines stay in top condition.
This means your customers no longer need to worry about missing key maintenance tasks. Machines perform more reliably, repairs are handled proactively, and productivity remains high.
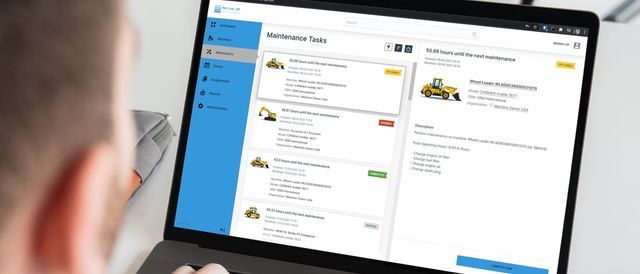
Less downtime, lower costs, happier customers
With online maintenance planning, OEMs can streamline their service processes and enhance customer relationships.
- Improved compliance: Ensure that maintenance schedules are followed strictly based on real machine usage.
- Lower costs: Streamline workflows and resource planning for more efficient maintenance processes, reducing repair costs.
- Increased dealer turnover: Dealers can see more business as service appointments are better planned and managed.
- Stronger customer relationships: Stay in touch with customers by proactively scheduling maintenance and boosting loyalty.
For machine owners, online maintenance planning helps keep machines running efficiently while reducing downtime and repair costs.
- Less downtime: Automated notifications help prevent missed maintenance, keeping machines running smoothly.
- Lower repair costs: Proactive planning reduces the risk of costly breakdowns.
- Increased productivity: Maintenance is scheduled at optimal times, avoiding unexpected delays.